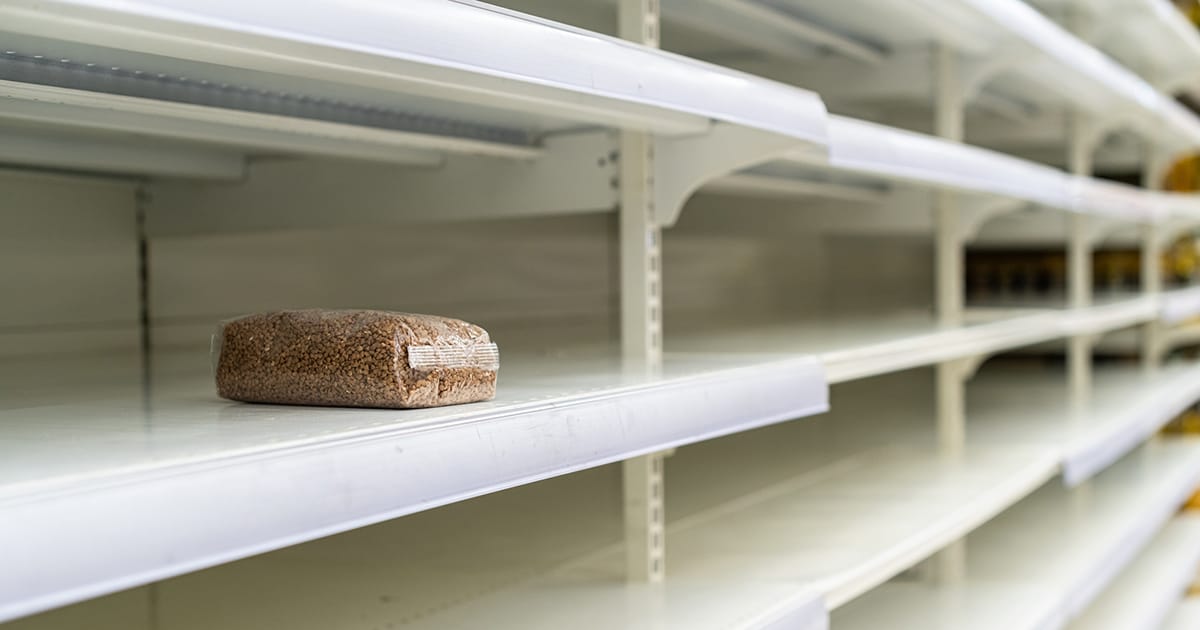
While there is no food shortage problem in Antigua and Barbuda, Information Minister Melford Nicholas says the Cabinet has already set its sight on that possibility.
He says the government will continue to monitor global supply chain issues.
Nicholas was speaking at the post-Cabinet news conference this morning.
Wondering why everything from cars and refrigerators to books and toys is in short supply?
Blame the fouled-up supply chain that connects manufacturers around the world with the makers and assemblers of their component parts, as well as with the consumers and businesses that buy the finished goods. The problem emerged shortly after the COVID-19 pandemic struck, and it’s seemed to get only worse since then.
How did we get into this mess? And why isn’t it getting better? The Times reached out to some supply chain experts, and here are their answers.
What, exactly, is ‘the supply chain’?
Manufacturers in the U.S. and the rest of the industrialized world have long outsourced the production of common and low-cost products to China and other low-wage countries. But starting in the 1970s, companies outsourced the production of an increasing number of more sophisticated products, often using multiple contractors to produce and then assemble the components.
Here’s how it typically works: A company based in the U.S. will design and put the finishing touches on a product but will turn to one or more foreign manufacturers for raw materials and components if that will significantly cut the cost to build and deliver it. For example, according to the American University Auto Index, roughly half of each Dodge Ram 1500 truck that rolled out of a U.S. auto plant last year came from outside the U.S. and Canada.
Global supply chains are especially prevalent in durable goods (such as cars and appliances), tech products (such as cellphones and computers), clothing, footwear, textiles, furniture and plastic goods. And although most U.S. imports come from China, Mexico and Canada are also important links in the supply chain here, as are a number of Asian and European countries.
What caused the problem?
In a word, COVID-19. The pandemic whirled up a toxic brew of forces that triggered and then exacerbated the shipping logjam.
The first blow came when many of the Chinese plants that build parts or assemble goods for global manufacturers were shut down by coronavirus outbreaks. Similar disruptions soon spread across the globe, affecting both manufacturers and the logistics companies that ship, store and deliver their goods.
After a brief COVID-related recession, however, demand for goods grew quickly, as people shifted to online buying and took up new habits (a surge in home-improvement projects, for example, boosted demand for appliances and construction materials).
Manufacturers face a “perfect storm” of issues, said Nick Vyas, executive director of the Kendrick Global Supply Chain Institute at the USC Marshall School of Business.
Labor, transportation and logistics costs are up, there’s reduced capacity because of the problems all along the supply chain, and there’s a finite amount of resources across the board, including the number of containers and amount of manufacturing capacity.
“We might be able to buffer against one type of risk or two types of risk, but it’s the fact that all these challenges are happening at the same time,” said Nicole DeHoratius, an adjunct professor of operations management at the University of Chicago’s Booth School of Business.
The pandemic is not entirely to blame. Robert Handfield, the Bank of America professor of supply chain management at North Carolina State University, said that “warehouse, distribution and truck driver shortages were bad before COVID.”
The delays caused by the backlog in deliveries have been particularly disruptive to companies that operate with small inventories and rely on “just in time” shipments to fill orders. To avoid that pitfall, some companies are ordering extra supplies and components as a precaution, increasing the strain on the distribution system.
Another factor: Concerns about the spread of COVID-19 and its variants have made it harder for trucks to cross borders. A report Monday by Moody’s Analytics said the differences among countries’ efforts to control the coronavirus have gummed up the movement of transportation workers at ports and other freight hubs, contributing to a problem that will get worse before it gets better.
And it’s not easy to restart factories after they’ve been shut down to stem surges in coronavirus cases. Raw materials back up, and it can take weeks to restart production, Vyas said.
“The supply chain is a system,” he said. “When you create shocks from the supply to the demand side and that continues to happen, the system isn’t getting enough time to reset and recalibrate.”
Why are cargo ships waiting to be unloaded at the ports?
West Coast ports were barely keeping up with the growth in freight before the pandemic and had no ability to absorb disruption, said Ayman Omar, an associate professor at American University’s Kogod School of Business. The pandemic has only worsened the situation, including a shortage of trucks to haul cargo containers to their destinations.
There were 64 ships in a holding pattern near the ports of Los Angeles and Long Beach Thursday.
Some trucking industry executives blame higher federal unemployment benefits, which ended in September, for the driver shortage. Omar said that the benefits might have contributed to the problem in the early months of the pandemic, but the issue now is competition coming from transportation start-ups hungry for market share. Drivers come and go at trucking companies at an alarmingly high rate — turnover was more than 90% at large firms in the last quarter of 2020.
Without enough trucks to carry them off, containers piled up on docks, and more kept coming — each new ship brings in 10,000 to 21,000 containers. And with the ports of Los Angeles and Long Beach unable to handle the growing number of ships, vessels were spending about as much time waiting to anchor and unload — about two weeks — as it would take a ship to cross the Pacific, said Robert Khachatryan, chief executive of Freight Right Global Logistics of La Crescenta.
Compounding the problem is the lack of transparency and information sharing, which makes it impossible for the manufacturers and importers who rely on the ports to see problems developing in advance and route around them, Omar said.
Advertise with the mоѕt vіѕіtеd nеwѕ ѕіtе іn Antigua!
We offer fully customizable and flexible digital marketing packages.
Contact us at [email protected]
Every thinking person knew this 18 months ago. The momey and food is essential to the control mechanism. These puppets we have mascarading as caring people should eel the wrath of the people.
*feel
If this persists, We may be looking at a two tier society where the rich are sustained while the poor and middle class have to fight for survival. Even consider the possibility of total systemic failure in the financial markets.
Not “if” it continues. That is and has always been the plan(demic) from day 1.
You may be looking at a two tiered society?
You’re already there and have been there for a while
They are determined to usher in a Digital ID, the
vacciness are paramount to that end.
To the unvaxxed: You have to make sure you’re prepared for this engineered crisis. Food scarcity is one of their weapon to make you comply. If and when governments takes control of the food supply, they can decide only the vaxxed can receive food. It’s already happening in France, where some supermarkets won’t allow the unvaxxed to enter. It’s going to be a long hard road if you’re not totally prepared.
Well I heard about the food shortage possibility and supply chain issues on several “conspiracy theories”.
Not one of the cabinet members are starving for food. We on the other hand can’t work because they shoving poison in our bodies.
Government has gotten out of hand and too strong. If we don’t take back power from the government, we and our children will be forever fucked.
This reeks of low calibre, high rent Antiguan politicians trying to be in things again, hitching their narrative to world events.
Most of these ships are piled up outside…California…where procedures are more important that people. If they push these draconian rules on truckers (the most independent and free thinking people you can find), this is going to get worse. If 20% of truckers quit, the US will lose 15% of it’s cargo capabilities. Ironically, Florida is open for business and begging them to come, but I guess they don’t want Florida to look to good these days, especially considering their radical (but successful) views on COVID management.
🤔food shortage. If I knew this was coming I would get me some farmlands with a lake🚣
Comments are closed.